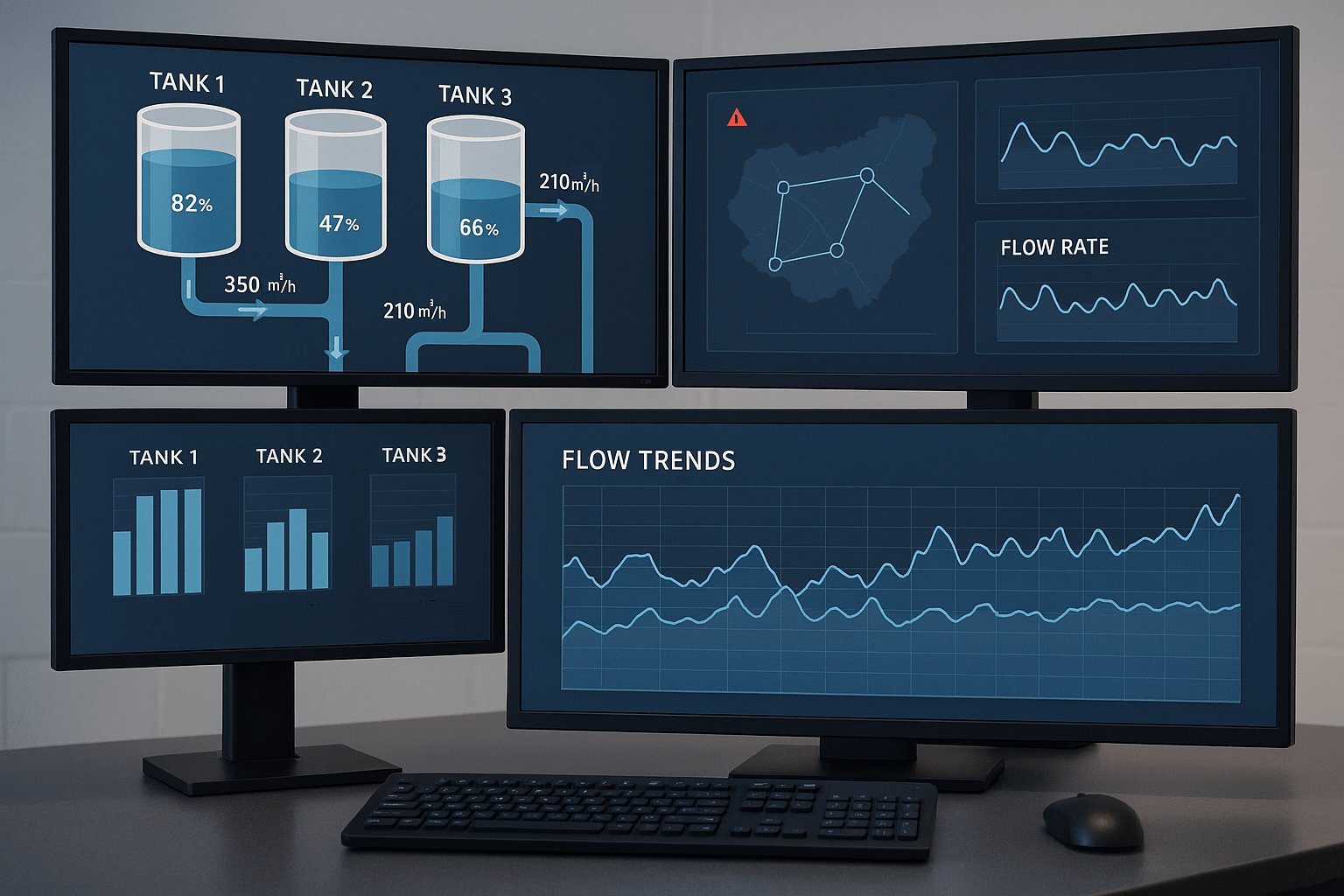
In the rapidly evolving industrial world, the demand for more efficient and environmentally conscious fluid storage systems is growing stronger every day. While traditional tanks and systems served their purpose in the past, the industry is now embracing advanced solutions that not only improve performance but also align with global sustainability goals. This evolution represents a shift not just in technology, but in the way industries approach fluid storage as a whole.
Digital Transformation in Storage: The Role of Smart Tech and IoT
The incorporation of the Internet of Things (IoT) is changing the game for fluid storage, transforming static storage systems into highly dynamic, interconnected systems. With real-time data collected via sensors and connected devices, operators can continuously monitor essential factors like pressure, temperature, fluid levels, and contaminants. This data empowers operators to respond swiftly to any discrepancies, optimize fluid usage, and ensure that systems adhere to safety and environmental standards.
One of the most powerful aspects of IoT technology is predictive analytics, which uses historical and real-time data to identify potential issues before they become problems. This can include detecting leaks, wear, or impending failures, allowing for proactive maintenance that reduces downtime, increases equipment lifespan, and cuts costs.
Moreover, IoT integration supports remote monitoring, enabling facility managers to monitor multiple sites from centralized locations or mobile devices. This reduces the need for on-site staff and enhances workplace safety, especially in hazardous environments. Automated systems further ensure swift responses to critical issues, minimizing the risk of accidents and ensuring uninterrupted operations.
Eco-Friendly Materials: Advancing Sustainability with GRP and FRP
The materials used for fluid storage are also evolving as industries strive for more sustainable solutions. Traditional materials like steel and concrete have long been standard but are often prone to corrosion, heavy weight, and high maintenance costs. In contrast, Glass Reinforced Plastic (GRP) and Fiber Reinforced Plastic (FRP) offer a compelling alternative, combining lightweight flexibility with exceptional durability and corrosion resistance.
These composite materials are less prone to degradation, even in harsh environments, making them ideal for fluid storage systems that deal with aggressive chemicals or extreme weather. Their resistance to corrosion also minimizes leaks, contamination, and structural failure. Furthermore, GRP and FRP tanks are easier and cheaper to transport and install, reducing logistics costs, especially in remote or challenging locations.
The long lifespan of these materials reduces the need for frequent repairs and replacements, lowering maintenance costs and environmental impact. GRP and FRP are also aligned with sustainability goals, offering recyclable options and contributing to more efficient fluid management and less material waste over time.
Modular Tank Systems: Flexibility and Scalability for Growing Demands
In an era where adaptability is critical, modular tank systems are revolutionizing fluid storage. Unlike fixed-size traditional tanks, modular tanks are designed with interchangeable panels or sections that can be expanded, disassembled, or reconfigured based on evolving needs. This flexibility is invaluable for industries with fluctuating fluid storage requirements.
Modular tanks are ideal for growing operations, allowing businesses to scale storage capacity as needed without constructing new infrastructure. They also fit into spaces where traditional tanks may not work, including urban environments or remote locations. These tanks are highly portable, allowing for quick assembly and disassembly in temporary applications like disaster relief or military operations, making them a cost-effective and reusable solution.
Moreover, modular designs contribute to sustainability by reducing waste. Rather than discarding outdated tanks, modular systems allow for component reuse and reconfiguration, supporting a circular economy approach and reducing the environmental footprint of fluid storage.
Automation and Robotics: Enhancing Precision and Safety
The use of automation and robotics is transforming fluid storage operations, enhancing both precision and safety. Robotic systems are increasingly used for tasks such as inspections, cleanings, leak detection, and valve testing—tasks traditionally carried out manually. By using robotics, businesses can minimize worker exposure to hazardous environments, improving safety and ensuring compliance with health standards.
Automation also delivers unparalleled precision and consistency, eliminating human error and ensuring that processes are performed exactly as needed every time. Automated systems work continuously, improving efficiency and reducing downtime. For instance, robotic cleaning systems can operate during off-hours or without emptying tanks, extending asset uptime and improving overall facility productivity.
Integration with IoT platforms and predictive maintenance tools allows for real-time monitoring and data analysis, further optimizing maintenance strategies and ensuring that any issues are addressed before they escalate. This combination of robotics and automation is setting the stage for more efficient and cost-effective fluid storage management.
Sustainable Energy Integration: Reducing Environmental Impact
Fluid storage systems are increasingly incorporating renewable energy solutions, playing an active role in sustainable energy strategies. Solar-powered pumps, for example, offer an off-grid solution for fluid distribution, particularly in remote regions where conventional energy sources may be unreliable. These pumps reduce fuel consumption and greenhouse gas emissions, helping businesses lower both their carbon footprint and operational costs.
Energy recovery systems, which capture and repurpose energy otherwise lost during fluid processing, are another key innovation. These systems enable businesses to reuse energy for other processes, driving down energy consumption and reducing costs over time. Rainwater harvesting systems are also gaining popularity, helping industries reduce their reliance on municipal water sources by capturing and storing rainwater for non-potable uses like irrigation and cooling.
By integrating sustainable energy technologies, businesses are not just reducing their environmental impact—they are also optimizing fluid storage systems for greater efficiency and future-proofing their operations against rising energy costs and tightening environmental regulations.
Predictive Maintenance: Preventing Issues Before They Occur
In a data-driven world, predictive maintenance has become a game-changer for fluid storage systems. Rather than relying on reactive maintenance or scheduled interventions, predictive maintenance uses real-time data and advanced algorithms to anticipate potential problems before they happen. Sensors embedded in storage systems monitor key parameters like pressure, temperature, and vibration, alerting operators to anomalies that may indicate wear or failure.
This proactive approach extends the life of critical assets, reduces emergency repair costs, and minimizes downtime, which can be costly and disruptive. Predictive maintenance also aligns with sustainability goals by reducing waste, lowering energy consumption, and optimizing the lifespan of storage systems.
Remote Monitoring: Empowering Control from Anywhere
As fluid storage networks expand, remote monitoring and management are becoming indispensable. Centralized control systems allow operators to manage multiple sites from a single dashboard, providing real-time data on tank levels, pressures, temperatures, and other vital metrics. This level of connectivity is especially valuable for hard-to-reach sites, such as offshore platforms or remote field locations, where traditional inspections can be costly or dangerous.
Remote monitoring also reduces travel costs and environmental impact by minimizing the need for on-site inspections. When combined with predictive and preventive maintenance strategies, remote systems enable intelligent decision-making and operational efficiency.
Looking to the Future: The Next Generation of Fluid Storage
The future of fluid storage is defined by smarter, more sustainable solutions. With intelligent monitoring systems, eco-friendly materials, and renewable energy integration, the industry is embracing innovation and environmental stewardship. Solico Tanks, a leader in GRP panel tank manufacturing since 1966, is driving this transformation. Through ongoing innovation and a commitment to sustainability, Solico is setting new benchmarks for the future of fluid storage, providing advanced systems that meet the needs of a rapidly evolving industrial landscape, Contact Solico Tanks to learn more!