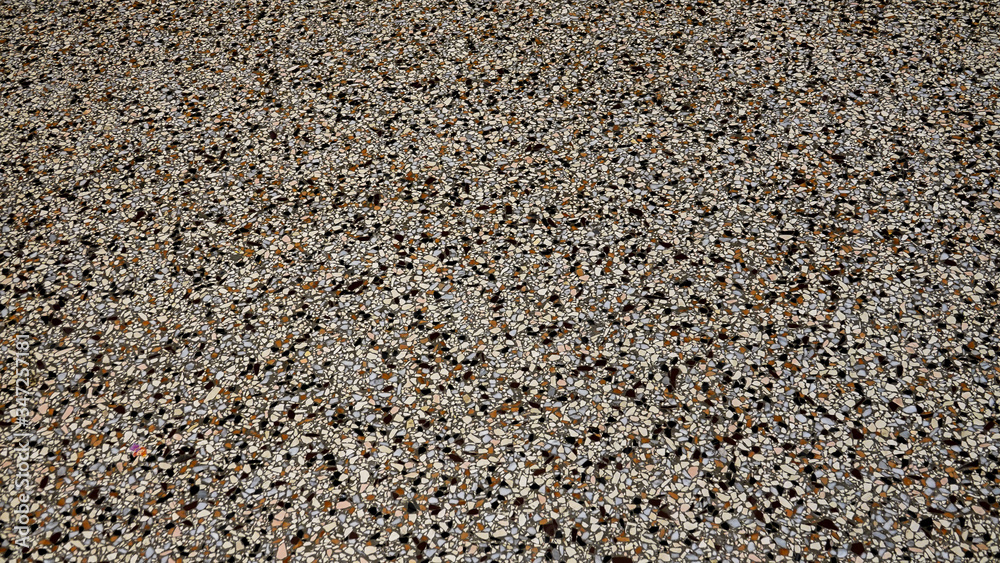
Polyaspartic coatings have gained significant popularity in various industries due to their remarkable properties such as fast curing times, excellent adhesion, and high durability. However, like any chemical product, proper precautions must be taken during application to ensure both safety and optimal performance. Whether you’re a seasoned professional or a DIY enthusiast, understanding and implementing the necessary precautions is crucial. In this comprehensive guide, we’ll delve into the essential precautions to consider when applying polyaspartic coatings to achieve the best results while maintaining safety standards.
Understand the Product:
Before applying polyaspartic coatings, it’s imperative to thoroughly understand the product’s specifications, application procedures, and safety data provided by the manufacturer. This includes information on proper ventilation requirements, recommended protective gear, and handling procedures. Familiarizing yourself with these details will help prevent accidents and ensure compliance with safety regulations.
Ensure Adequate Ventilation:
Proper ventilation is paramount when working with Construction Chemicals. These coatings often contain volatile organic compounds (VOCs) that can pose health risks if inhaled in high concentrations. Therefore, it’s essential to work in well-ventilated areas, such as outdoor spaces or rooms with ample airflow. If working indoors, use exhaust fans or air filtration systems to minimize exposure to fumes.
Wear Personal Protective Equipment (PPE):
When handling polyaspartic coatings, always wear appropriate PPE to protect yourself from potential hazards. This typically includes safety goggles, chemical-resistant gloves, protective clothing, and respiratory masks rated for organic vapors. Additionally, avoid wearing clothing or accessories that can easily absorb or trap chemicals, such as fabric gloves or loose-fitting clothing.
Follow Mixing Instructions Precisely:
Polyaspartic coatings typically require precise mixing ratios and procedures to ensure proper curing and adhesion. Deviating from the manufacturer’s instructions can result in subpar performance or even product failure. Use calibrated measuring tools and follow the recommended mixing sequence meticulously to achieve the desired results. Avoid guesswork or shortcuts that could compromise the integrity of the coating.
Monitor Environmental Conditions:
Environmental factors such as temperature, humidity, and substrate moisture content can significantly impact the application and curing of polyaspartic coatings. Before application, assess the ambient conditions and ensure they fall within the recommended ranges specified by the manufacturer. Extreme temperatures or humidity levels can affect coating viscosity, drying times, and overall finish quality. Make necessary adjustments or wait for suitable conditions before proceeding with the application.
Take Precautions Against Contamination:
Contamination from dust, debris, or foreign particles can compromise the adhesion and appearance of polyaspartic coatings. Thoroughly clean and prepare the substrate surface according to industry standards before applying the coating. Use appropriate cleaning agents, abrasives, and techniques to remove any contaminants, grease, or previous coatings that may hinder adhesion. Additionally, take measures to prevent airborne debris from settling onto freshly applied coatings during the curing process.
Implement Proper Application Techniques:
Achieving a smooth, uniform coating requires employing proper application techniques. Whether spraying, rolling, or brushing, ensure consistent coverage and avoid over-application or pooling, which can lead to uneven drying and curing. Follow a systematic application pattern, overlapping each pass slightly to prevent streaks or missed areas. Take care to maintain a wet edge to facilitate seamless blending between sections and minimize visible seams or lap lines.
Allow Sufficient Curing Time:
Rushing the curing process can compromise the performance and longevity of polyaspartic coatings. Allow ample time for the coating to cure fully according to the manufacturer’s recommendations before subjecting it to foot traffic, vehicular traffic, or other stresses. Premature exposure to moisture, chemicals, or mechanical abrasion can result in surface imperfections, reduced durability, or adhesion failures. Exercise patience and plan the project timeline accordingly to ensure optimal results.
Dispose of Waste Properly:
Proper disposal of unused product, empty containers, and cleaning materials is essential for minimizing environmental impact and adhering to regulatory requirements. Follow local regulations regarding the disposal of hazardous waste and recycling of containers. Avoid pouring excess product or cleaning solvents down drains or onto the ground, as this can contaminate soil and water sources. Instead, collect and dispose of waste materials responsibly through designated channels.
Educate and Train Personnel:
If working in a professional setting, ensure that personnel involved in the application of polyaspartic coatings receive adequate training and education on safety protocols, product handling, and application techniques. Provide ongoing support and supervision to reinforce proper practices and address any concerns or questions that may arise. Investing in training not only promotes a safer work environment but also enhances the quality and consistency of the finished coatings.
In conclusion, applying polyaspartic coatings requires careful consideration of various precautions to ensure both safety and effectiveness. By understanding the product, following recommended procedures, and prioritizing safety measures, you can achieve professional-quality results while minimizing risks to yourself, others, and the environment. Always prioritize safety and adherence to best practices to maximize the performance and longevity of polyaspartic coatings in your projects.