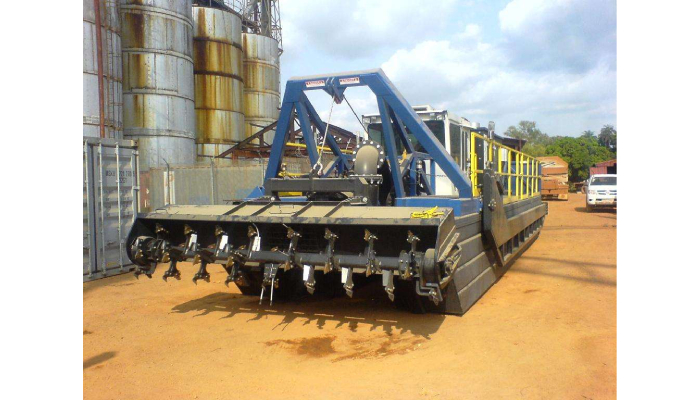
Maintaining your mine tailings dredge regularly is key to keeping it working well and lasting longer. Because tailings are abrasive and heavy, daily checks of engine oil, coolant, and lubrication on moving parts like cutterheads help prevent breakdowns. Weekly inspections of hydraulic hoses and fan belts catch issues early before they become costly repairs. Over time, changing filters and monitoring pumps for clogging reduce wear from sand and silt. Using abrasion-resistant materials and non-clog pump designs also protect the equipment. Staying consistent with these tasks not only extends the dredge’s lifespan but also helps avoid downtime that could delay mining projects or harm the environment.
Dredge Maintenance and Handling Abrasive Tailings
Handling abrasive mine tailings dredge demands a focused approach to dredge maintenance, with daily inspections of pumps, cutterheads, and liners to catch early signs of wear. Using abrasion-resistant materials like high-chrome alloys or rubber coatings on these components helps reduce damage and extend their service life. Daily lubrication of all moving parts is crucial to minimize friction and prevent premature failures caused by abrasive slurry. Operators should monitor tailings consistency closely and adjust dredging parameters to avoid excessive abrasion, which can rapidly degrade equipment. Regular cleaning of pumps and pipelines prevents sediment buildup that leads to clogging and increased wear. It’s important to replace worn parts promptly to stop damage from spreading, and protective coatings on metal surfaces help guard against corrosion in the wet, abrasive environment. Seals and gaskets also need scheduled checks since abrasive slurry can cause leaks, compromising dredge efficiency. Training operators to recognize abrasion damage early and report it helps maintain operational readiness. Keeping detailed records of wear rates on key components enables accurate forecasting of replacements, ensuring the dredge remains reliable and downtime is minimized.
Daily and Weekly Maintenance Tasks for Your Dredge
Start each day with a thorough visual inspection of your dredge, looking closely for cracks, missing parts, or any structural damage that could worsen during operation. Before firing up the engine, check oil and coolant levels to ensure everything is within the recommended range, this prevents overheating and engine wear. During startup, listen carefully for unusual noises or vibrations that might signal mechanical issues early on. Daily lubrication is crucial: apply grease to bearing blocks, the cutterhead, and all moving parts to reduce friction and wear caused by abrasive tailings. Confirm that all controls and safety systems are fully functional to avoid operational hazards. On a weekly basis, drain water separators to remove moisture that can contaminate oil systems and cause damage. Inspect fan belts and pulleys for proper tension and signs of wear, loose or worn belts can lead to sudden breakdowns. Examine hydraulic hoses for leaks, cracks, or abrasions, replacing any damaged hoses promptly to maintain hydraulic efficiency. Also, check the dredge structure for corrosion or damage, especially in areas exposed to high wear or harsh conditions. Keeping detailed records of all inspections and maintenance actions helps track the dredge’s condition over time, making it easier to spot recurring issues and plan repairs before failures occur. Regular attention to these daily and weekly tasks builds a solid foundation for your dredge’s long-term reliability and performance.
- Conduct a visual inspection for cracks, missing parts, and structural damage each day.
- Check engine oil and coolant levels every morning before operation.
- Lubricate bearing blocks, cutterhead, and other moving parts daily to prevent wear.
- Test engine start-up for unusual noises or vibrations indicating potential issues.
- Drain water separators weekly to remove moisture from oil systems and prevent contamination.
- Inspect fan belts and pulleys weekly for proper tension and signs of wear.
- Examine hydraulic hoses weekly for leaks, cracks, or abrasions and replace if necessary.
- Check dredge structure weekly for corrosion or damage, especially in high-wear zones.
- Confirm all controls and safety systems function properly during daily checks.
- Record all inspections and maintenance actions to maintain a clear service history.
Monitoring Critical Dredge Components Regularly
Regular monitoring of your mine tailings dredge’s essential components is key to spotting issues before they escalate. Start with daily checks of engine oil pressure and temperature to catch early signs of engine stress, which helps prevent costly breakdowns. Alongside this, verify coolant levels daily and inspect the cooling system for leaks or blockages to avoid overheating. Hydraulic oil quality should be inspected weekly through visual checks and, when possible, lab analysis to detect contamination that can harm pumps and motors. Bearing blocks and the cutterhead require daily lubrication to maintain smooth operation in abrasive conditions, neglecting this leads to accelerated wear. Dredge pumps must be examined regularly for clogging or damage to impellers and housings, as these components endure constant exposure to sand and silt. Fan belts and pulleys need weekly inspection for wear or misalignment, which can cause mechanical failure if ignored. Safety decals, cables, and emergency stop systems should be reviewed at least every 1000 hours to ensure operational safety and compliance. Structural parts deserve attention too: look for corrosion or cracks during inspections to maintain the dredge’s integrity. Using vibration monitoring tools, where available, adds a layer of early detection for bearing or pump issues by identifying unusual vibrations. Lastly, make sure all seals and gaskets are intact to prevent slurry leaks, which can damage internal components and cause environmental hazards. Consistent adherence to these monitoring steps helps maintain dredge performance and extends equipment life in demanding mine tailings environments.
Hour-Based Service Intervals and Key Checks
Maintaining your mine tailings dredge according to hour-based service intervals is crucial for its reliable performance and longevity. At 100 hours, start by changing the engine oil and filter, then inspect the main dredge pump and lubricate all essential parts to prevent early wear. When the dredge hits 250 hours, replace fuel and hydraulic oil filters, and conduct thorough checks on bearing blocks, impellers, the cutterhead, and pulleys for signs of wear. The 500-hour mark calls for another fuel filter change and a detailed inspection for corrosion, cracks, or excessive wear across all components. By 1000 hours, perform a hydraulic oil analysis to detect contaminants that could damage the system; also inspect and replace pulleys, cables, and safety decals as needed. It’s important to follow manufacturer recommendations precisely to keep your warranty valid and ensure optimal performance. Logging all maintenance by hour intervals helps track equipment health over time and supports predictive maintenance, allowing you to plan spare parts procurement efficiently. If your dredge operates in harsh or highly abrasive environments, increase inspection frequency to catch issues early. Always have trained personnel carry out these service tasks to maintain consistency and quality. Finally, review actual operating conditions along with hour intervals to adjust maintenance schedules, ensuring your dredge stays in top condition despite varying workloads and environmental challenges.
Overcoming Challenges Unique to Tailings Dredges
Mine tailings dredges face unique challenges that require tailored solutions to keep them running smoothly. Abrasive wear is a major concern since the tailings contain sharp sand and silt that quickly erode pumps, impellers, and cutterheads. To combat this, using parts made from abrasion-resistant materials and coatings is essential. Pumps often clog due to debris, so selecting non-clog designs like open rotors or vortex pumps helps prevent blockages and reduces strain on equipment. Regular and frequent inspections are critical to catch early signs of wear or damage before they cause major failures. Maintenance schedules should be adjusted to the harsh environment and continuous operation demands, often requiring more frequent checks than other dredging applications. Operator training plays a key role too, as skilled operators can recognize early warning signs of stress and manage abrasive tailings carefully. Efficient cleaning routines to clear sand, silt, and debris from pumps and pipelines reduce the risk of clogging and wear. Keeping a stock of critical wear parts on hand minimizes downtime when replacements are needed. High turbidity in tailings ponds means seals must be well-maintained to prevent leaks during operations and maintenance, protecting the environment. Using precision dredging tools and monitoring systems helps reduce environmental impact and keeps operations safer. Finally, careful planning of maintenance downtime is necessary to avoid disrupting mining schedules and meeting project deadlines.
Using Abrasion-Resistant and Non-Clog Pump Designs
Selecting the right pump materials is crucial for handling abrasive mine tailings. High chrome or rubber liners help resist wear caused by abrasive particles, extending pump life significantly. Pumps designed with open rotors or vortex impellers are preferred because they handle solids up to 11 inches without clogging, reducing downtime due to blockages. Regular inspections are necessary to catch early signs of erosion, cracks, or damage on impellers and housings. Daily lubrication of pump seals and bearings helps avoid premature failure and keeps the pump running smoothly. Frequent cleaning prevents debris buildup that can lead to clogging or excessive wear. Replacing worn components promptly is essential to avoid costly breakdowns. Proper pump alignment and secure mounting reduce vibration and uneven wear, improving overall durability. Using pumps that match the slurry characteristics of your dredge ensures better performance and less stress on components. Training operators to recognize signs of clogging or overload can prevent damage caused by improper use. Finally, maintaining detailed maintenance and performance records allows for ongoing optimization and early detection of potential issues.
Lubrication and Wear Prevention Techniques
Proper lubrication is essential to protect your mine tailings dredge from the abrasive slurry that constantly wears down moving parts. Daily greasing of bearing blocks, cutterheads, and other exposed components helps reduce friction and prevent premature failure. Always use lubricants recommended by manufacturers, focusing on water-resistant and high-pressure grease types that can withstand slurry exposure without breaking down. Before applying grease, clean the lubrication fittings thoroughly to avoid introducing dirt, which can cause further abrasion. It’s important to inspect lubrication points daily to ensure there is sufficient grease and no contamination. Over-lubrication should be avoided, as excess grease can attract abrasive particles that cause damage rather than prevent it. Monitoring bearing temperatures and vibration levels provides early warning signs of lubrication issues, helping to catch problems before they lead to costly breakdowns. Incorporate lubrication tasks into your daily and scheduled maintenance checks to avoid neglect. Training maintenance staff on the correct lubrication procedures specific to dredging equipment ensures consistent and effective application. Additionally, keep lubricant storage clean and protected to maintain the quality and performance of greases over time.
Spare Parts Management and Operator Training
Maintaining a well-organized inventory of critical wear parts like impellers, seals, belts, and filters is essential to minimize downtime during repairs. Tracking the consumption rates and lead times for these parts helps prevent unexpected stockouts, especially when urgent replacements are needed. Setting reorder points based on average wear and operational hours keeps the inventory balanced and ready. Operator training plays a crucial role in daily maintenance routines; teaching them how to spot early signs of equipment problems can prevent small issues from escalating. Regular refresher courses ensure the team stays current with best practices and any changes in equipment or procedures. Using checklists and maintenance logs promotes consistency and accountability in executing maintenance tasks. Encouraging open communication between operators and maintenance staff allows for prompt reporting and troubleshooting of issues. Documenting training sessions and tracking operator competencies enhances accountability and helps identify areas needing improvement. Collaborating with manufacturers or service providers for specialized training can provide deeper insights and technical support. Finally, fostering awareness of environmental and safety protocols during both operation and maintenance ensures compliance and protects personnel and the surrounding ecosystem.
Incorporating Technology for Efficient Maintenance
Integrating technology into your mine tailings dredge maintenance can significantly boost efficiency and reduce unexpected downtime. Scheduled maintenance logging systems help keep track of service intervals and component conditions, making it easier to follow maintenance plans and avoid missed checks. Lab analysis of hydraulic oil and lubricant samples allows early detection of contamination, preventing damage caused by degraded fluids. Using vibration monitoring and diagnostic tools can predict potential component failures before they become critical, enabling timely repairs. Technologies like GPS, sonar, and camera-equipped dredges improve dredging precision, which not only enhances operational efficiency but also limits environmental impact by minimizing disturbance. Modular dredging systems make maintenance simpler by improving access to key parts and allowing quick replacement of modules. In sensitive or hard-to-reach areas, remotely operated or diver-assisted dredging offers a safer and more precise approach to maintenance tasks. Digital checklists and mobile apps provide real-time reporting and help ensure compliance with maintenance schedules. Condition monitoring sensors installed on critical components deliver continuous data, alerting operators to any abnormalities. Training your staff on these technologies is crucial to maximize their benefits. Regularly reviewing the collected data helps optimize maintenance schedules, reducing unplanned downtime and extending the life of your dredge equipment.
Environmental and Safety Measures During Maintenance
Before starting any maintenance work on your mine tailings dredge, make sure all local environmental regulations are followed and that your dredging permits are up to date. This helps avoid legal issues and ensures your operation respects environmental standards. During maintenance, minimize sediment disturbance to prevent turbidity spikes in nearby water bodies, which can harm aquatic life. Use drip trays and containment systems to catch oil or hydraulic fluid leaks, preventing contamination of soil and water. Wearing the right personal protective equipment (PPE) is essential to protect maintenance personnel from hazards like chemical exposure or mechanical injuries. Regularly inspect safety features such as cables, emergency stop buttons, and alarms to confirm they work correctly and provide quick response options in case of emergencies. Maintenance teams should be trained in spill response and environmental best practices to handle any accidental releases promptly and effectively. Schedule maintenance activities to avoid periods critical to local wildlife, such as breeding or migration seasons, to reduce ecological impact. Dispose of waste oils, filters, and worn parts in line with environmental guidelines to prevent harmful substances from entering the environment. Lastly, keep detailed records of all environmental compliance actions and safety inspections as part of your maintenance logs to demonstrate responsible management and support regulatory audits.