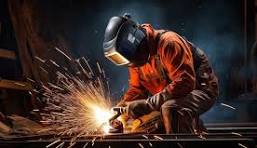
Welding rods are an essential component in the welding process, and understanding the differences between different types can greatly impact the quality of your welds. 7018 welding rod and 7018 A1 are two commonly used electrodes in welding applications. While they may seem similar at first glance, there are important differences between the two that can affect their performance and suitability for specific welding tasks.
7018 Welding Rod:
7018 welding rod is a low-hydrogen, iron powder electrode that is known for its high tensile strength and excellent weldability. It is designed for use in all positions and produces smooth, clean welds with minimal spatter. The 7018 electrode is commonly used in structural welding, pipeline welding, and heavy fabrication projects.
One of the key features of the 7018 welding rod is its low moisture content, which helps prevent hydrogen cracking in the weld. This makes it an ideal choice for welding applications where high-strength and crack-resistant welds are required. The 7018 electrode also has a stable arc and good penetration, making it suitable for welding thick materials.
7018 A1 Welding Rod:
7018 A1 welding rod is a variant of the 7018 electrode that is specifically designed for welding high-strength steels, including high-carbon and high-alloy steels. The “A1” designation indicates that this electrode has been modified to provide greater strength and toughness in the weld.
One of the main differences between 7018 and 7018 A1 welding rods is the composition of the flux coating. 7018 A1 electrodes typically contain additional alloying elements, such as manganese and silicon, that enhance the mechanical properties of the weld. This results in welds that are more resistant to cracking and have improved ductility and impact strength.
In addition, 7018 A1 welding rods are often recommended for applications where the base metal has a high carbon content, as they can help prevent the formation of hard and brittle microstructures in the heat-affected zone. This makes them a preferred choice for welding materials that are prone to cracking, such as cast iron and high-carbon steels.
Overall, while both 7018 and 7018 A1 welding rods share many similarities, the key differences lie in their composition and intended applications. The 7018 electrode is a versatile choice for general welding tasks, while the 7018 A1 electrode is better suited for high-strength and high-alloy steels that require superior mechanical properties in the weld.
Conclusion
In conclusion, understanding the differences between 7018 welding rod and 7018 A1 is essential for selecting the right electrode for your welding needs. Whether you are working on structural projects or welding high-strength materials, choosing the appropriate welding rod can make a significant difference in the quality and durability of your welds. In addition to their chemical composition and welding characteristics, 7018 and 7018 A1 welding rods may also differ in terms of their certifications and specifications. Welders should always refer to the manufacturer’s guidelines and welding procedures to ensure that they are using the correct welding rod for their specific welding application.
Read More (Click Here)