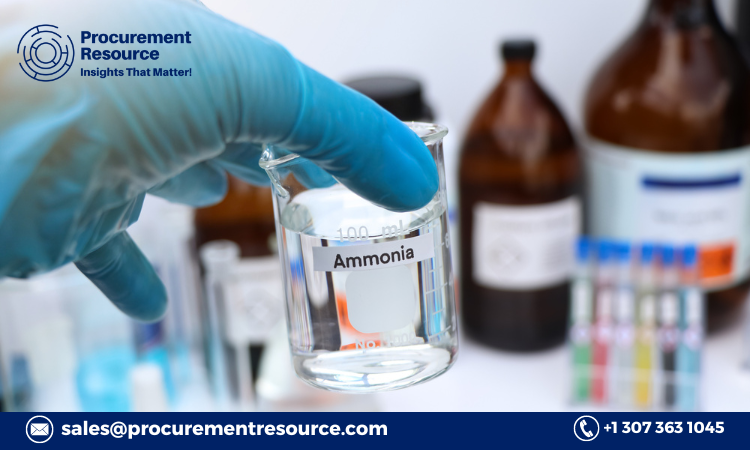
Ammonia (NH3) is a vital chemical in the industrial world, primarily used as a precursor for fertilizers. Its production is a cornerstone of the chemical industry, with applications ranging from agricultural products to industrial cleaning agents and even refrigeration. Understanding the ammonia production process, the associated manufacturing techniques, and the production costs is essential for businesses and researchers involved in the chemical sector.
Ammonia Production Process
The production of ammonia is predominantly carried out using the Haber-Bosch process, a method developed in the early 20th century by Fritz Haber and Carl Bosch. This process synthesizes ammonia from nitrogen and hydrogen, using high temperature and pressure in the presence of a catalyst.
Request For Sample: https://www.procurementresource.com/production-cost-report-store/ammonia/request-sample
- Raw Material Sourcing
- Nitrogen: Sourced from the air, which contains approximately 78% nitrogen.
- Hydrogen: Typically obtained from natural gas (methane) through a process called steam reforming. Alternative sources include coal gasification and electrolysis of water.
- Steam Reforming
- In this initial step, natural gas (methane) reacts with steam to produce hydrogen and carbon monoxide.
- Reaction: CH4 + H2O → CO + 3H2
- Water-Gas Shift Reaction
- The carbon monoxide produced in the steam reforming step reacts with steam to produce additional hydrogen and carbon dioxide.
- Reaction: CO + H2O → CO2 + H2
- Carbon Dioxide Removal
- The carbon dioxide is removed from the gas mixture using a solvent like monoethanolamine (MEA).
- Nitrogen and Hydrogen Mixing
- The purified hydrogen is mixed with nitrogen (extracted from the air) in a ratio of 3:1.
- Ammonia Synthesis (Haber-Bosch Process)
- The nitrogen and hydrogen mixture is compressed and passed over an iron catalyst at high temperatures (400-500°C) and pressures (150-300 atmospheres) to produce ammonia.
- Reaction: N2 + 3H2 ↔ 2NH3
- Ammonia Recovery
- The ammonia is separated from unreacted gases through condensation and is then collected for further use or storage.
Manufacturing Report
Key Equipment and Technology
- Reformers:
- Steam reformers convert methane into hydrogen and carbon monoxide. These are critical components due to their role in hydrogen production.
- Compressors:
- High-pressure compressors are essential for achieving the required pressures in the ammonia synthesis loop.
- Reactors:
- The ammonia synthesis reactor is where nitrogen and hydrogen combine to form ammonia. These reactors must withstand high pressures and temperatures.
- Heat Exchangers:
- Heat management is crucial in the ammonia synthesis process. Heat exchangers recover and utilize the heat generated during the reaction, improving energy efficiency.
- Cooling and Separation Units:
- After synthesis, ammonia needs to be separated from the gas mixture. Cooling units condense ammonia, which is then separated from unreacted gases.
Innovations and Efficiency Improvements
- Catalyst Development:
- Advances in catalyst technology have led to more efficient and selective catalysts, increasing ammonia yield and reducing energy consumption.
- Process Integration:
- Integrating various process steps to recover and reuse energy has significantly improved the overall efficiency of ammonia plants.
- Carbon Capture and Storage (CCS):
- Modern ammonia plants are increasingly incorporating CCS technologies to reduce carbon dioxide emissions, making the process more environmentally friendly.
Production Cost Analysis
Cost Components
- Raw Materials:
- Natural gas is the primary raw material, accounting for a significant portion of production costs. The price of natural gas can fluctuate based on market conditions, impacting overall production costs.
- Energy Costs:
- Ammonia production is energy-intensive, requiring substantial amounts of electricity and heat. Energy costs are influenced by regional energy prices and the efficiency of the production process.
- Labor and Maintenance:
- Skilled labor is required to operate and maintain the complex equipment used in ammonia production. Maintenance costs can be high due to the harsh operating conditions of the equipment.
- Capital Costs:
- The initial investment in constructing an ammonia plant is substantial, covering the cost of land, equipment, and infrastructure.
Cost Reduction Strategies
- Energy Efficiency:
- Improving energy efficiency through advanced technologies and process optimization can significantly reduce production costs.
- Feedstock Optimization:
- Utilizing alternative feedstocks, such as renewable hydrogen, can help mitigate the impact of natural gas price volatility.
- Operational Excellence:
- Implementing best practices in operation and maintenance can reduce downtime and maintenance costs, improving overall plant economics.
- Economies of Scale:
- Larger plants benefit from economies of scale, spreading fixed costs over a higher production volume, thus reducing per-unit production costs.
Conclusion
Ammonia production is a complex but essential industrial process with significant economic and environmental implications. The Haber-Bosch process remains the predominant method, supported by continuous technological advancements aimed at improving efficiency and sustainability. Understanding the intricacies of the production process, the key equipment involved, and the cost dynamics is crucial for stakeholders in the ammonia industry. By focusing on innovation and efficiency, the industry can continue to meet global demand while addressing environmental challenges.