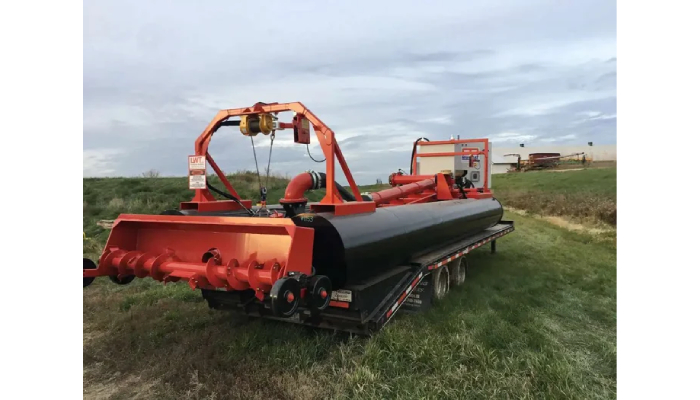
Integrated Automated Dredge Control Systems combine monitoring, control, and automation of dredging operations to improve vessel performance. By integrating subsystems like cutting heads, pumps, and navigation controls, these systems offer real-time adjustments that enhance precision and efficiency. Automation features support constant depth and production dredging while reducing manual interventions. This leads to lower fuel consumption and operational costs alongside safer working conditions by minimizing human errors. Environmental benefits include reduced sediment spread and compliance with emission targets. Although full autonomy is still limited due to project complexity and regulatory concerns, ongoing advancements in AI and sensor technology promise gradual improvements in dredging automation for both newbuilds and retrofit vessels.
Overview of Integrated Automated Dredge Control Systems
Integrated Automated Dredge Control Systems (IADCS) bring together various vessel subsystems into a single platform to manage dredging operations more effectively. By combining controls for cutting equipment, dredge lines, pumps, and navigation, these systems offer real-time monitoring and precise control that improves overall vessel performance. Automation reduces the need for constant manual input by handling complex and repetitive tasks, which helps minimize human error and enhances safety on board. IADCS continuously collect and process data related to dredging volume, vessel position, and equipment status, enabling operators to make timely adjustments during operations. These systems can be installed on new vessels or retrofitted to existing ones, making them adaptable to different fleet needs. Beyond operational benefits, integrated automation supports environmental compliance by optimizing dredging accuracy and reducing sediment disturbance. As dredging technology evolves alongside autonomous shipping trends, IADCS play a key role in advancing safer, more efficient, and environmentally responsible vessel operations.
Core Components and Automated Functions
Integrated Automated Dredge Control Systems rely on a range of core components designed to ensure precise and efficient dredging operations. Real-time sensors continuously monitor key parameters such as cutter head position, slurry pump performance, and winch tension, providing immediate feedback to the control system. Automated side winch control plays a crucial role in maintaining exact dredge line positioning, which is essential for accurate excavation and minimizing wear on equipment. Constant depth dredging functions automatically adjust vessel operations to maintain target excavation depths, reducing the risk of over- or under-dredging. Similarly, constant production dredging manages slurry pump speeds to deliver a stable output volume, optimizing material handling and fuel consumption. Advanced profile dredging software guides the excavation process to follow predefined seabed contours, ensuring compliance with project specifications. Start-up and shut-down sequences are automated to streamline equipment readiness and safe shutdown, reducing manual intervention and potential errors. Control systems vary from standalone units managing individual functions to sophisticated client-server architectures that integrate multiple subsystems and enable centralized data management.
Precision and Efficiency Benefits
Integrated Automated Dredge Control Systems ensure dredging operations stay within exact depth and profile tolerances, eliminating costly over-dredging and minimizing under-dredging that can lead to rework. By precisely controlling cutter speed and slurry pumping, these systems streamline cycle times and maintain consistent production rates. Optimized equipment operation reduces fuel consumption, while coordinated start and stop sequences cut idle times, further lowering operational costs. Real-time data feedback allows for quick adjustments to maintain ideal dredging conditions, improving accuracy and helping meet strict contract specifications. This precision also lessens environmental impact by reducing sediment disturbance. Overall, automation boosts efficiency by cutting manual labor, enhancing process flow, and delivering reliable, controlled dredging performance.
Safety Improvements Through Automation
Automation in integrated dredge control systems significantly reduces risks related to human fatigue, distraction, and judgment errors, which are common causes of accidents on dredging vessels. By automating repetitive and hazardous tasks such as controlling cutter heads and pumping operations, crew exposure to dangerous environments is minimized, enhancing overall safety. Early stages of automation help ease the crew’s workload, allowing them to focus on more complex decision-making rather than routine monitoring. Automated emergency shutdowns are critical safety features that protect both personnel and equipment by promptly responding to system faults or dangerous conditions. Remote monitoring capabilities further limit the need for personnel to be physically present in high-risk dredging zones, reducing the chance of injury. The consistency provided by automated control systems eliminates incidents caused by manual operation inconsistencies, maintaining safer working conditions. Safety protocols are embedded directly into the automation logic, ensuring operational limits are enforced without relying solely on human vigilance.
Environmental Impact and Compliance
Integrated Automated Dredge Control Systems play a crucial role in minimizing environmental impact while ensuring regulatory compliance. Precision dredging enabled by these systems reduces sediment dispersion and water turbidity, which helps protect marine ecosystems and maintains water quality. Automated controls prevent over-dredging, limiting seabed disturbance and preserving habitats. By optimizing operational parameters such as cutter head speed and dredge depth, these systems reduce fuel consumption, leading to lower greenhouse gas emissions. This supports vessel compliance with International Maritime Organization (IMO) targets for carbon reduction by 2030 and 2050. Real-time environmental monitoring can be integrated to adjust dredging activities based on water conditions, further reducing ecological impact. Automation also facilitates the adoption of decarbonization strategies, including electric drives and energy-saving features, which contribute to a smaller carbon footprint. Data logging capabilities provide comprehensive records for environmental audits and reporting, ensuring transparency and adherence to regulations. Additionally, reduced operational errors lower the risk of accidental spills or discharges, safeguarding marine environments. Growing environmental regulations are driving the increased adoption of these automated dredge controls, making them an essential component in sustainable dredging operations.
Optimizing Vessel Performance with Automation
Integrated automation systems play a crucial role in enhancing vessel performance by combining precise control with real-time data insights. Newbuild dredging vessels now come equipped with fully integrated automation, managing marine and dredging operations seamlessly to improve productivity and operational accuracy. Meanwhile, retrofit automation solutions extend the life and capabilities of older vessels, allowing them to keep pace with modern efficiency standards. Automation enables vessels to optimize positioning during dredging, reducing fuel consumption and minimizing project durations. By coordinating equipment operation such as cutter heads, pumps, and winches, automated systems ensure smooth workflows that boost production reliability across varied dredging tasks. Energy reuse and electrical drive integration further cut fuel use, contributing to lower emissions and operational costs. Continuous condition monitoring supports predictive maintenance, reducing downtime and unplanned repairs. Automation also offers flexibility to adapt quickly to changing project requirements, ensuring vessels maintain peak performance regardless of task complexity. Overall, the integration of automated dredge control systems results in operational and environmental gains that elevate vessel efficiency, safety, and sustainability in a competitive industry.
Industry Trends and Real-World Examples
Leading dredging companies like Van Oord, Jan De Nul, and Boskalis are actively investing in integrated automated dredge control systems to enhance vessel performance. Newbuild dual-fuel trailing suction hopper dredgers (TSHDs) now often come equipped with advanced automation that improves precision, fuel efficiency, and environmental compliance. Retrofitting older vessels remains common, with notable examples including the Liberty Island TSHD, built in 2002, and the Oranje TSHD, which underwent length extension and automation upgrades. These projects demonstrate how automation can extend vessel life and boost productivity. The dredging industry is also influenced by offshore oil and gas technologies and the rise of autonomous shipping, which bring new ideas for automation and remote operation. Adoption of automation is accelerating, driven partly by stricter environmental and safety regulations that demand more precise dredging and reduced emissions. Artificial intelligence and machine learning are beginning to be integrated into dredge control systems, enabling smarter decision-making and adaptive operations.
Automation Levels in Dredging and Shipping
The International Maritime Organization (IMO) defines four levels of autonomous shipping, ranging from onboard automated processes with crew present to fully autonomous vessels without human intervention. Most dredging vessels today operate within the first two levels: onboard automation paired with remote control, where crew members remain onboard to oversee and manage operations. Full autonomy in dredging remains limited because of the complex and dynamic marine environment, as well as safety concerns that require human judgment and quick decision-making. Remote control is sometimes used for specific dredging tasks, but always under human supervision to handle unexpected situations. Automation in dredging mainly assists operators rather than replaces them, incrementally improving functions like cutter head control, dredge depth maintenance, and pump regulation. As autonomy levels rise, vessels need robust fail-safe systems and strong cybersecurity measures to protect against failures and external threats. Regulatory frameworks for autonomous dredging vessels are still evolving, influenced by the type of project and the operational risks involved. Looking ahead, semi-autonomous or unmanned dredging vessels may become more common, especially for repetitive or lower-risk tasks, but human oversight will likely remain essential for the foreseeable future.