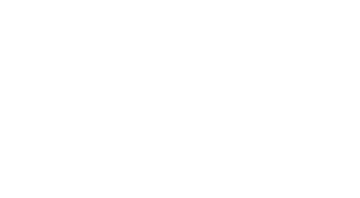
China has emerged as a global powerhouse in manufacturing advanced metal laser cutting machines, combining cost-effectiveness with cutting-edge technology. For industries ranging from automotive to aerospace and heavy machinery, choosing the right China metal laser cutter manufacturer is critical for ensuring precision, durability, and operational efficiency.
Why China Leads in Metal Laser Cutter Manufacturing
-
Advanced Technology Integration: Chinese manufacturers invest heavily in fiber laser and CO2 laser technology, improving cutting speed and accuracy.
-
Competitive Pricing: Cost advantages due to large-scale production and lower labor costs.
-
Customization & Innovation: Flexible manufacturing to meet diverse industrial needs and integration with automation.
-
Strong Supply Chain: Access to high-quality components like laser sources, CNC systems, and optics.
Key Features of Metal Laser Cutters from China
Feature | Description | Industry Benefit |
---|---|---|
Fiber Laser Technology | Uses solid-state lasers with high beam quality and efficiency. | Precise cuts, less maintenance. |
High Cutting Speed | Capable of cutting thick and thin metals rapidly. | Increased productivity, less downtime. |
CNC Integration | Computer numerical control for exact cutting patterns. | Complex designs, repeatability. |
Multi-Metal Capability | Cuts stainless steel, carbon steel, aluminum, brass, copper, etc. | Versatility across industries. |
Energy Efficiency | Modern lasers consume less power with higher output. | Cost savings, sustainable operation. |
User-Friendly Interface | Touchscreen controls with software for easy programming. | Reduced operator training time. |
Safety Features | Protective enclosures, emergency stops, and ventilation systems. | Compliance with international safety standards. |
How to Select the Right China Metal Laser Cutter Manufacturer
Selecting a manufacturer involves more than just price comparison. It requires evaluating expertise, product quality, service, and reliability. Below are critical factors to consider:
1. Technical Expertise & Experience
Look for manufacturers with a proven track record in laser technology innovation and extensive experience in metal cutting machinery. This ensures the machines incorporate the latest advancements and robust engineering.
2. Product Quality & Certifications
Check for internationally recognized certifications such as ISO 9001 for quality management and CE marking for safety compliance. Manufacturers with rigorous quality control deliver reliable, long-lasting machines.
3. Customization & After-Sales Support
A reputable manufacturer offers tailored solutions fitting your specific metal types, thickness, and production scale. Also, robust after-sales service including installation, training, and technical support is essential to minimize downtime.
4. Customer Reviews & Industry Reputation
Analyze feedback from previous clients to gauge real-world performance and manufacturer responsiveness. Industry awards or recognition highlight authority and trustworthiness.
5. Technology Partnerships
Manufacturers collaborating with global laser source providers (e.g., IPG Photonics, Raycus) often deliver superior laser cutters due to access to premium components.
Frequently Asked Questions (FAQs)
Q1: What types of metals can China metal laser cutters handle?
A: Most machines can cut a wide variety of metals including stainless steel, carbon steel, aluminum, brass, copper, titanium, and alloys with thickness ranging from 0.2mm up to 30mm or more depending on the model.
Q2: How does fiber laser compare to CO2 laser in metal cutting?
A: Fiber lasers offer higher cutting speeds, better energy efficiency, and require less maintenance, especially for thin to medium thickness metals. CO2 lasers can cut thicker materials but at a slower rate and higher operating cost.
Q3: Is training necessary to operate metal laser cutters?
A: Yes, professional training is recommended to maximize efficiency and safety. Most Chinese manufacturers provide comprehensive operator training as part of their after-sales package.
Q4: How long is the typical warranty period for these machines?
A: Warranty periods usually range from 1 to 3 years, covering key components such as laser sources and CNC systems. Extended service contracts can be negotiated.
Q5: What about maintenance and spare parts availability?
A: Reliable manufacturers maintain a stock of critical spare parts and provide remote diagnostics and onsite service to ensure minimal disruption.
Comparative Table: Top Metal Laser Cutter Types from Chinese Manufacturers
Machine Type | Best For | Cutting Thickness Range | Typical Industries | Cost Range (USD) |
---|---|---|---|---|
Fiber Laser Cutter | High precision thin metals | 0.2mm – 20mm | Electronics, Automotive | $25,000 – $120,000 |
CO2 Laser Cutter | Thick metals, complex designs | 1mm – 30mm | Aerospace, Heavy machinery | $30,000 – $150,000 |
Hybrid Laser Cutter | Multi-material, flexibility | 0.2mm – 25mm | Fabrication, Tooling | $40,000 – $130,000 |
Portable Handheld Laser | On-site cutting/repair | Up to 6mm | Construction, Maintenance | $5,000 – $15,000 |
The Impact of EEAT Principles in Choosing Your Manufacturer
Expertise
The manufacturer’s depth in laser physics, CNC programming, and metallurgy translates directly into machine precision and operational efficiency. Verify their team qualifications and R&D investments.
Experience
Manufacturers with long-standing presence demonstrate proven processes, continuous innovation, and adaptation to market demands. Ask about their history, flagship products, and client case studies.
Authoritativeness
Recognition by industry bodies, patents on laser technology, and partnerships with leading tech firms strengthen manufacturer authority and product credibility.
Trustworthiness
Transparent business practices, solid warranty terms, and positive client testimonials build trust. Choose manufacturers who provide clear documentation and certifications.
Enhancing Operational Efficiency with a Chinese Metal Laser Cutter
Incorporating a metal laser cutter from a reliable Chinese manufacturer can optimize production workflows:
-
Speed: Fast processing reduces lead time for orders.
-
Precision: Tight tolerances cut material waste and improve product quality.
-
Automation: CNC integration enables unattended operation, freeing labor resources.
-
Cost Reduction: Energy-efficient lasers and minimal tooling lower operational costs.
Interactive Checklist: Are You Ready to Choose a China Metal Laser Cutter Manufacturer?
-
Have you identified your material types and thickness requirements?
-
Have you evaluated manufacturers’ technology and innovation capabilities?
-
Are quality certifications and safety standards verified?
-
Do you have clarity on warranty, service, and spare parts support?
-
Have you reviewed client feedback and industry reputation?
-
Did you confirm pricing fits your budget including potential customizations?
This structured and comprehensive overview equips you with expert-level knowledge to navigate the China metal laser cutter manufacturer market confidently, ensuring you make a data-driven decision that aligns with your industrial goals and quality expectations.