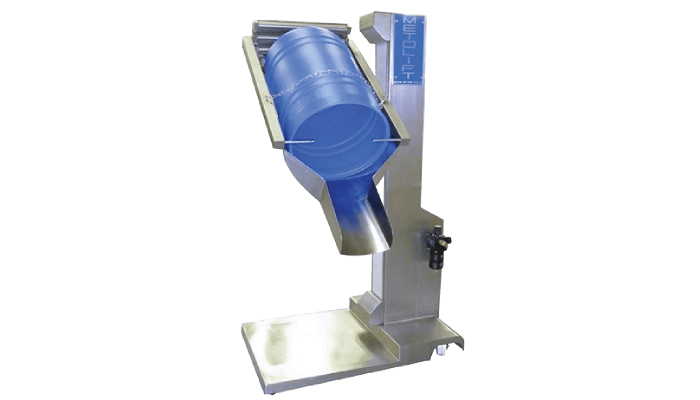
Proper maintenance of drum handling equipment is essential to ensure safety and extend its lifespan. Start with regular inspections to catch any visible damage like cracks or worn parts, paying close attention to clamps, chains, and wheels. Cleaning the equipment often helps remove grease and chemicals that cause wear, while lubricating moving parts prevents rust and keeps everything running smoothly. Store the gear in dry sheltered spots to avoid corrosion or deformation. Always operate within rated load limits and make sure operators are properly trained. Scheduling routine maintenance with timely repairs and keeping detailed records can prevent downtime. Following these steps supports safe, reliable drum handling every time.
Effective Cleaning and Lubrication Practices
Regular cleaning of drum handling equipment is crucial to keep it working smoothly. Dirt, grease, and chemical residues can build up and cause parts to stick or wear out faster. Use cleaning agents that won’t harm the materials of the equipment, check compatibility before applying. Pay special attention to wheels and rollers, as debris accumulation can lead to uneven movement or damage. For hard-to-reach spots, use brushes, rags, or low-pressure air to avoid hurting delicate components. After cleaning, always wipe down metal surfaces to remove moisture and prevent rust. Lubrication is equally important for moving parts like wheel bearings, hinge joints, pivots, and rollers. Applying the right lubricant according to the manufacturer’s schedule helps reduce friction and extend the life of these components. Avoid over-lubricating, since excess lubricant can attract dust and grime, speeding up deterioration instead of slowing it down. Store your cleaning and lubrication supplies properly to keep them effective and safe for use. Finally, make sure operators and maintenance staff are trained on proper cleaning and lubrication techniques. Consistent care ensures the equipment stays reliable and safe for daily drum handling tasks.
- Remove dirt, grease, and chemical residues frequently to prevent buildup that can hinder equipment function.
- Use cleaning agents that are safe and compatible with the equipment’s materials to avoid damage.
- Apply lubricants to moving parts such as wheel bearings, hinge joints, pivots, and rollers to reduce friction and wear.
- Follow recommended lubrication schedules and use the types of lubricants specified by manufacturers.
- Clean wheels and rollers thoroughly to avoid debris accumulation that causes uneven movement.
- Wipe down metal surfaces after cleaning to prevent moisture retention and rust formation.
- Avoid over-lubrication which can attract dust and grime leading to faster deterioration.
- Use brushes, rags, or low-pressure air to clean hard-to-reach areas without damaging components.
- Store cleaning and lubrication materials properly to maintain their effectiveness and safety.
- Train operators and maintenance staff on correct cleaning and lubrication techniques to ensure consistency.
Proper Storage Tips for Drum Handling Tools
Storing drum handling equipment properly is key to extending its lifespan and ensuring safe use. Keep all tools in dry, sheltered areas to reduce exposure to moisture and corrosive substances that cause rust and deterioration. Avoid stacking equipment, as this can lead to bending or warping of frames and clamps. Instead, arrange tools so each piece rests securely without pressure from others. Secure stored items to prevent accidental movement or falls, which might damage components or create safety hazards. For equipment stored long-term, especially in outdoor or humid environments, apply protective covers or coatings to shield against environmental damage. Maintain clear and organized storage spaces to allow easy access and prevent accidents during retrieval. Store smaller parts like drum clamps separately in labeled bins or compartments to avoid misplacement and damage. Label storage locations clearly so tools are returned properly, minimizing loss and confusion. Never place heavy items on top of drum handling tools, as this can deform their shape and affect function. Also, ensure the storage floor is clean and free of debris that could damage wheels or cause uneven resting surfaces, which may lead to premature wear or instability during use. Regularly inspect stored equipment for early signs of rust or damage, so you can address issues before they worsen.
Safe Load Handling and Operation Guidelines
Proper training is essential to ensure operators understand the equipment’s load limits and correct handling techniques. Always adhere strictly to the rated load capacity to prevent structural failures or accidents. Before moving or lifting drums, verify that loads are balanced and securely fastened to avoid shifts that could cause spills or tip-overs. Only use the equipment on surfaces compatible with its wheels and frame design; uneven or unsuitable floors increase the risk of tipping or damaging the equipment. Follow the manufacturer’s instructions carefully when lifting, tilting, or transporting drums to maintain stability and control. Avoid sudden movements such as quick starts, stops, or sharp turns, as these can destabilize both the load and the equipment. When working in confined or busy spaces, employ spotters or guides to help maneuver heavy or awkward loads safely. Inspect drums for any visible damage or leaks before handling to prevent spills or hazardous situations. Keep pathways clear of obstacles, debris, or slippery spots to allow smooth, safe transit. Ensure emergency stop functions and controls are easily accessible and operational, so operators can quickly respond if something goes wrong during handling.
Routine Maintenance and Timely Repairs
Establishing and following a maintenance schedule is essential for keeping drum handling equipment in good working order. This schedule should include regular inspections, servicing, and timely replacement of worn or damaged parts using manufacturer-approved components to ensure safety and performance. It’s important to tighten all bolts, nuts, and fasteners routinely, as vibration and use can cause them to loosen over time. Lubricating moving parts such as hinges, rollers, and bearings during maintenance reduces friction and prevents premature wear, helping the equipment to operate smoothly. Cleaning the equipment thoroughly during maintenance not only keeps it in good condition but also makes it easier to spot hidden issues like cracks or corrosion that could lead to failure. Checking the alignment of moving parts and making necessary adjustments ensures efficient operation and prevents unnecessary strain on components. After any repair, testing safety features like locking mechanisms and brakes confirms they function correctly to protect operators. Keeping detailed records of all maintenance activities, repairs, and parts replaced is key for tracking equipment health and meeting compliance requirements. Additionally, scheduling periodic professional inspections can help identify problems beyond routine checks, catching potential issues early. Proper training for maintenance staff on correct repair procedures and tool use is critical to avoid causing damage during servicing and to maintain equipment longevity.
Safety Measures for Handling Drum Equipment
When handling drum equipment, wearing personal protective equipment like gloves, safety shoes, and eye protection is essential to reduce injury risks. Emergency stop and quick release mechanisms should be tested regularly to ensure they work properly in urgent situations. Clear signage displaying load capacities, operational instructions, and hazard warnings must be visible on all equipment to guide safe use. Only trained personnel should have access to drum handling areas, and operators must be physically capable and well-trained for their tasks. Avoid loose clothing or jewelry that could get caught in moving parts, and keep workspaces well-lit and free of clutter to prevent trips or collisions. Regular safety drills and reviews help maintain readiness, while educating workers on emergency procedures, including spill response, promotes a safer environment. All incidents or near-misses should be reported and investigated thoroughly to improve safety protocols continuously.
Troubleshooting Common Drum Equipment Issues
When drum handling equipment shows signs of sticking or stiff parts, start by cleaning the affected areas thoroughly and applying lubricant to reduce friction. Uneven, noisy, or wobbly movement often points to worn wheels or bearings; inspect these components carefully and replace them as needed to restore smooth operation. Broken clamps, locks, or latches should be repaired or swapped out immediately to keep the drum secure during handling. If you notice unusual noises or vibrations, investigate promptly to catch mechanical faults early before they lead to bigger problems. Feeling instability or hearing rattles means checking for loose fasteners or missing hardware, which can usually be tightened or replaced. For equipment using hydraulic or pneumatic systems, look for leaks or pressure drops that could impair functionality. Testing safety mechanisms regularly ensures they trigger correctly when faults occur. Make sure rollers and guides are properly aligned to avoid jams or uneven wear that could damage drums or equipment. Worn rubber or plastic parts that cause slipping should be replaced to maintain a good grip. When faced with complex issues that aren’t clear, consulting manufacturer support or technical documentation can provide specific guidance and solutions tailored to your equipment model.
Compliance with Safety Standards and Manufacturer Guidelines
Proper compliance with OSHA guidelines and local regulations is essential when maintaining drum handling equipment. Always refer to the manufacturer’s user manuals for detailed instructions on maintenance, operation, and safety to ensure that your procedures align with their specifications. Regular safety audits or inspections help verify that the equipment meets current standards and best practices, and keeping documentation of these efforts readily available is important for review by authorities or auditors. Procedures should be updated promptly whenever regulations or manufacturer recommendations change, preventing outdated practices that could risk safety or compliance. Any modifications or repairs must respect manufacturer warranties and certifications, avoiding actions that could void them. Training staff on relevant regulatory requirements ensures everyone involved understands their responsibilities in safe equipment use and upkeep. Clearly labeling equipment with load ratings and safety instructions, as required by standards, helps prevent misuse. Use only approved replacement parts to maintain the safety integrity of the equipment. If any non-compliance issues arise, report them immediately and take corrective action to avoid hazards or penalties. For example, replacing a worn chain with a non-approved substitute could compromise load capacity and violate safety regulations, so sticking to approved parts is vital for compliance and safety.
Training and Documentation for Equipment Users
Regular training sessions are essential to ensure all users understand proper operation, inspection, and maintenance of drum handling equipment. Hands-on demonstrations paired with practical exercises help reinforce correct techniques and safety procedures. It’s important to provide clear, accessible manuals, maintenance logs, and safety documents so users can easily reference key information whenever needed. Maintenance personnel should receive specialized training focused on troubleshooting, repairs, and record-keeping to maintain equipment reliability. Keeping detailed records of training attendance and activities supports compliance and helps identify when refresher courses are necessary. Encouraging users to promptly report any equipment problems or safety concerns fosters a proactive safety culture. Involving operators in risk assessments and gathering their feedback also promotes shared responsibility for equipment safety. Regularly updating training materials ensures the team stays informed about new equipment models or revised guidelines. Maintaining thorough documentation of equipment history, including inspections, repairs, and operator notes, supports ongoing maintenance efforts and helps prevent unexpected failures.