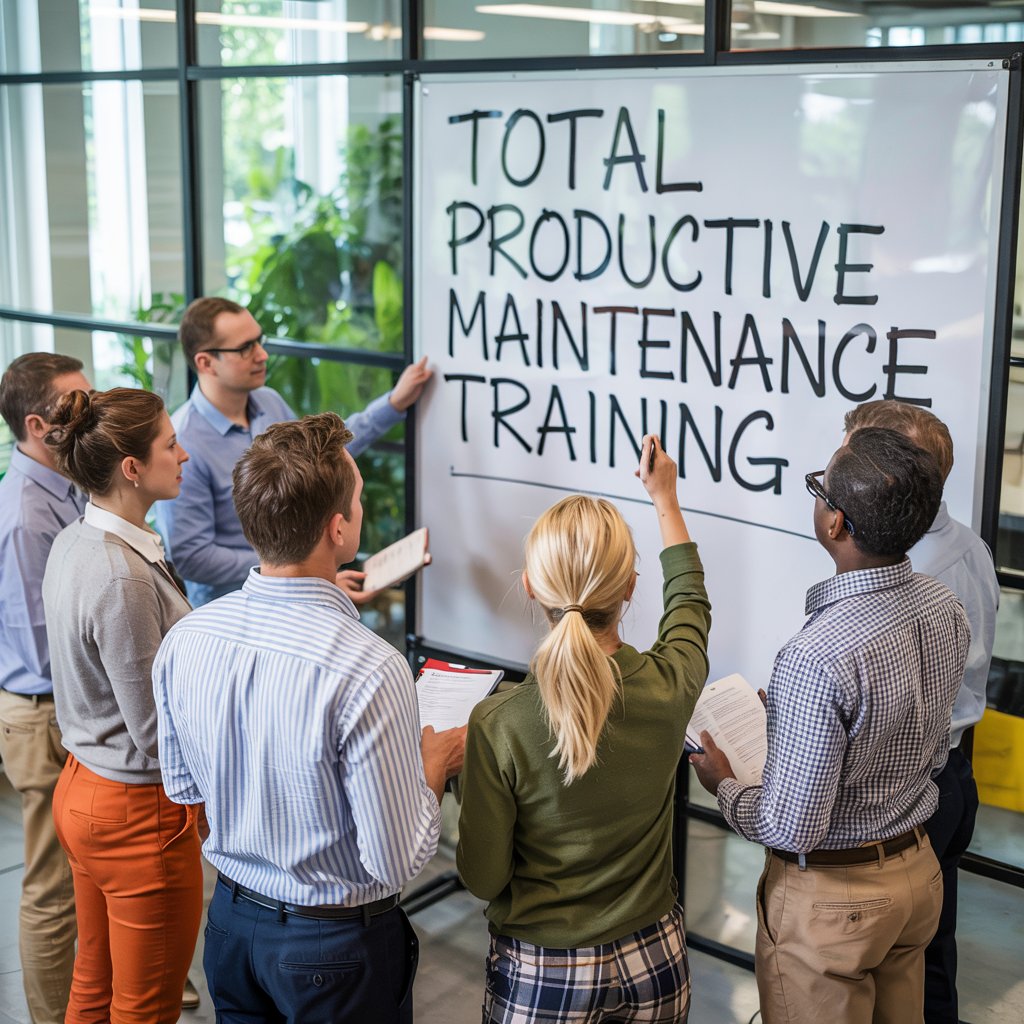
Total Productive Maintenance (TPM) is a comprehensive maintenance approach that focuses on maximizing equipment effectiveness, improving productivity, and fostering a culture of continuous improvement within organizations. Originally developed in Japan, TPM integrates maintenance into daily operations, emphasizing the proactive involvement of all employees.
This blog explores the key principles, benefits, and step-by-step implementation of TPM, helping businesses achieve operational excellence and minimize downtime.
Principles of Total Productive Maintenance (TPM)
TPM is built on fundamental principles that drive efficiency and effectiveness in equipment maintenance. These principles include:
1. Total Involvement
TPM encourages the active participation of all employees, from top management to frontline operators, in maintenance activities. By fostering shared responsibility, organizations create a culture of ownership and proactive problem-solving.
2. Proactive Maintenance
Rather than waiting for equipment failures, TPM focuses on preventive and predictive maintenance strategies. This proactive approach minimizes unexpected breakdowns and extends equipment lifespan.
3. Continuous Improvement (Kaizen)
TPM promotes an ongoing commitment to identifying inefficiencies and implementing small, incremental improvements that enhance productivity and safety.
4. Elimination of Waste and Losses
TPM aims to eliminate the six major losses in manufacturing, including equipment failures, setup and adjustment losses, idling and minor stoppages, reduced speed, defects in the process, and reduced yield.
5. Comprehensive Equipment Management
By integrating maintenance activities into daily operations, TPM ensures that machines are always operating at peak performance, reducing defects and rework.
Benefits of Total Productive Maintenance (TPM)
Organizations that implement TPM experience significant improvements in overall efficiency, product quality, and workplace morale. Some of the key benefits include:
1. Increased Equipment Reliability
TPM minimizes unplanned downtime by ensuring that equipment is well-maintained and operating efficiently, leading to consistent production output.
2. Higher Productivity Levels
With reduced machine failures and optimized workflows, organizations achieve higher production rates, meeting customer demands more effectively.
3. Cost Reduction
Preventive maintenance reduces repair costs, lowers spare parts consumption, and eliminates the need for frequent equipment replacements.
4. Improved Product Quality
By maintaining equipment in optimal condition, TPM ensures that products meet high-quality standards, reducing defects and waste.
5. Enhanced Workplace Safety
A well-maintained work environment reduces hazards associated with faulty equipment, creating a safer workplace for employees.
6. Employee Engagement and Skill Development
TPM fosters a sense of ownership among employees, empowering them with knowledge and skills to contribute to the organization’s success.
Implementation of Total Productive Maintenance (TPM)
Implementing TPM requires a structured approach to ensure a smooth transition and sustainable success. The following steps outline an effective TPM implementation strategy:
Step 1: Secure Leadership Commitment
Top management must support TPM initiatives by allocating resources, setting clear objectives, and fostering a culture of continuous improvement.
Step 2: Conduct a Baseline Assessment
Assess the current maintenance practices, equipment performance, and employee engagement levels. Identify key problem areas and set benchmarks for improvement.
Step 3: Form a TPM Implementation Team
Establish a cross-functional team consisting of representatives from maintenance, production, quality control, and management. This team will drive TPM initiatives and ensure alignment across departments.
Step 4: Develop a TPM Training Program
Educate employees on TPM principles, equipment handling, and preventive maintenance techniques. Training programs help build competency and foster a sense of responsibility among staff.
Step 5: Implement Autonomous Maintenance
Empower operators to take ownership of routine maintenance tasks such as cleaning, lubrication, and inspections. This prevents minor issues from escalating into major breakdowns.
Step 6: Establish a Preventive Maintenance Schedule
Develop a maintenance calendar based on equipment usage, performance data, and predictive maintenance techniques. Regular servicing ensures machines operate efficiently.
Step 7: Focus on Continuous Improvement (Kaizen)
Encourage employees to identify inefficiencies and suggest improvements. Implement small, incremental changes that enhance productivity and reduce waste.
Step 8: Integrate TPM with Quality Management
Ensure that TPM efforts align with quality control practices. Use root cause analysis to eliminate defects and improve product consistency.
Step 9: Monitor and Evaluate Performance
Track key performance indicators (KPIs) such as Overall Equipment Effectiveness (OEE), maintenance costs, and downtime reduction. Use data-driven insights to refine TPM strategies.
Step 10: Sustain TPM for Long-Term Success
To maintain TPM benefits, organizations should embed TPM into their corporate culture, conduct regular audits, and recognize employee contributions.
Conclusion
Total Productive Maintenance (TPM) is a powerful strategy that enhances equipment reliability, improves productivity, and fosters a culture of continuous improvement. By implementing TPM effectively, organizations can achieve higher efficiency, reduce costs, and create a safer work environment. With leadership commitment, employee involvement, and a structured approach, TPM can drive long-term success in manufacturing and other industries.
Start your TPM journey today with Unichrone and transform your maintenance strategies for a more efficient future!