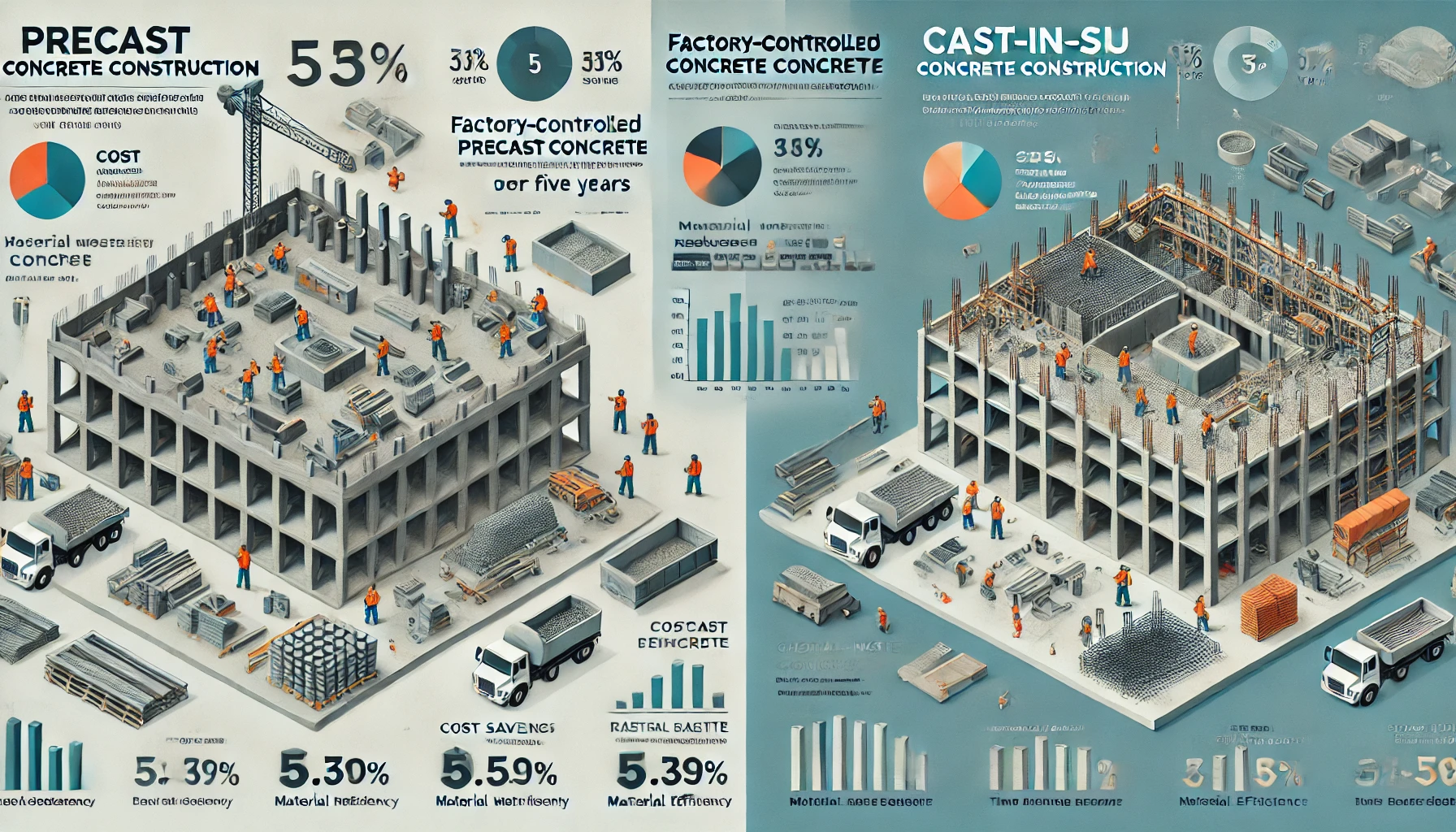
Precast vs. Cast-In-Situ Concrete: The Real Cost Battle
Imagine running a large-scale construction project. Deadlines loom, labor costs skyrocket, and delays eat into your budget. Every decision counts—especially the choice between precast concrete and cast-in-situ concrete.
Precast concrete is manufactured off-site under controlled conditions and assembled on-site, while cast-in-situ is poured and cured at the project location, demanding more labor and longer timelines.
But which method truly saves more money over five years? This deep dive into hard data—covering material efficiency, labor costs, and time savings—uncovers the ultimate cost-effective solution.
Key Findings: What the Data Shows
✅ Precast projects save up to 70.4% in total costs compared to cast-in-situ. ✅ Material wastage is significantly lower, reducing unnecessary expenses. ✅ 26% less manpower is required for precast, cutting labor costs. ✅ Construction time slashed by 40–50%, leading to faster project completion and quicker ROI. ✅ Cast-in-situ demands more skilled labor, increasing wages and extending timelines. ✅ Precast detailing services, like those from Tekance, optimize cost efficiency.
1. The Hidden Cost Saver: Reducing Material Wastage
Material wastage is a silent budget killer. Every wasted bag of cement, misplaced formwork, or weather-damaged structure adds up fast.
Precast Construction:
✔ Precision manufacturing minimizes waste. ✔ Excess materials can be reused, reducing procurement costs.
Cast-In-Situ Construction:
❌ On-site mixing leads to higher waste due to spills and errors. ❌ Weather factors can cause reworks, pushing costs higher.
💡 Bottom Line: Precast’s controlled quality results in significantly lower material costs.
2. Labor Costs: How Many Workers Do You Really Need?
Labor costs aren’t just about wages—they’re about how efficiently every dollar is spent.
Precast Concrete:
✅ 26% less manpower needed compared to cast-in-situ. ✅ No need for extra workers to set up and remove formwork. ✅ Fewer workers mean lower insurance and safety costs.
Cast-In-Situ Concrete:
❌ Requires skilled labor for pouring, curing, and supervision. ❌ More on-site personnel = higher indirect costs.
💡 Bottom Line: Precast’s reduced labor demand translates to lower payroll expenses.
3. Time Savings: Why Speed Matters in Construction
Time isn’t just money—it’s lost opportunities. Faster completion means a project can start generating revenue sooner.
Precast Concrete:
✅ 40–50% faster construction times. ✅ Components arrive ready-to-install, bypassing curing delays. ✅ Just-in-Time (JIT) delivery ensures seamless execution.
Cast-In-Situ Concrete:
❌ Requires curing time, scaffolding, and extensive site prep. ❌ Weather delays can prolong completion, escalating costs.
💡 Example: A high-rise project using precast finished six months early, saving millions in operational costs compared to a cast-in-situ counterpart.
4. Long-Term Cost Factors: Maintenance & Lifecycle
Construction costs don’t stop after completion—maintenance expenses add up over the years.
Precast Concrete:
✔ Higher durability due to controlled curing environments. ✔ Lower long-term maintenance costs—fewer cracks and structural issues.
Cast-In-Situ Concrete:
❌ Prone to cracks & repairs, especially in extreme climates. ❌ Ongoing maintenance eats into the original cost savings.
💡 Bottom Line: Over five years, precast requires significantly less maintenance expenditure.
5. Sustainability & Environmental Costs
Green building isn’t just good for the planet—it’s good for your budget.
Precast Concrete:
✅ Lower carbon footprint due to efficient, controlled production. ✅ Minimal waste and higher reusability.
Cast-In-Situ Concrete:
❌ Higher emissions from on-site batching and transportation. ❌ More material waste, increasing disposal costs.
💡 Bottom Line: Sustainable construction isn’t just ethical—it reduces material and energy expenses.
6. Real-World Cost Comparison: Who Wins?
A five-year study of large-scale infrastructure projects found:
Precast Construction:
✔ Total cost savings: 70.4% ✔ Construction time reduced by: 45% ✔ Labor costs cut by: 26%
Cast-In-Situ Construction:
❌ Higher total costs due to labor and delays. ❌ Weather-dependent schedule extended completion timelines.
📊 The verdict is clear: Precast consistently outperforms cast-in-situ across all cost factors.
Optimizing Precast with Tekance Detailing Services
Switching to precast is smart—but optimizing it for cost savings requires expert detailing and planning.
That’s where Tekance comes in. Our precast detailing services ensure:
✔ Accurate shop drawings to minimize material waste. ✔ Seamless structural alignment to reduce rework. ✔ Optimized project scheduling for maximum efficiency.
With Tekance’s expertise, your precast project will be faster, cheaper, and more efficient than ever.
FAQs
Is precast always cheaper than cast-in-situ?
Not always. The initial investment in molds and transportation can be higher. But long-term labor and time savings make it the more cost-effective option.
Does precast concrete have better durability?
Yes. Factory-controlled curing enhances strength, reducing cracks and defects.
Are there cases where cast-in-situ is better?
Yes. For custom designs with intricate geometries, cast-in-situ may offer more flexibility.
Final Verdict: The Smartest Cost-Saving Choice?
If your project prioritizes budget efficiency, labor savings, and faster completion, precast concrete is the clear winner.
And with Tekance’s precast detailing services, you can maximize your savings even further.
👉 Ready to transform your construction costs? Contact Tekance today.
Learn about Best TMT Bars for Construction: Strength, Durability, and Re