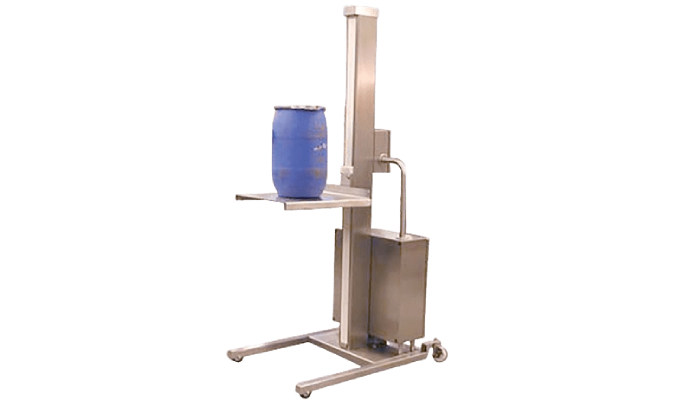
Using drum handling equipment brings several advantages to the workplace. First, it boosts safety by lowering injury risks tied to manual lifting and awkward postures. Workers experience less physical strain since mechanical aids handle heavy drums with ease. This also speeds up operations, making tasks quicker and more precise, which helps productivity overall. Storing drums becomes easier too, as specialized tools allow better organization in limited spaces. Although initial costs exist, the long-term savings from fewer injuries and improved efficiency pay off. Plus, equipment protects drum contents from damage or spills while offering flexible options for lifting, tilting, or transporting drums in various situations.
1. Enhanced Workplace Safety with Drum Handling Equipment
Drum handling equipment plays a key role in improving safety by reducing the need for manual lifting, which lowers the chance of back injuries among workers. Using mechanical aids ensures drums are moved and placed steadily, helping to prevent slips, trips, and falls that often happen with unstable loads. Secure clamps and lifters keep heavy drums from tipping or rolling unexpectedly, minimizing accidents caused by dropped drums. These safer handling methods also reduce the frequency of musculoskeletal disorders linked to repetitive strain, protecting workers from long-term injury. Many drum handling tools come with built-in safety features such as locks and grips, adding extra security during operations. When equipment supports consistent and standardized handling practices, it becomes easier to follow workplace safety protocols and comply with health and safety regulations. Ultimately, safer environments result in fewer injury claims and less employee downtime, while boosting worker confidence and morale during drum operations.
2. Increased Operational Efficiency in Drum Movement
Using specialized drum handling equipment significantly speeds up the process of lifting, moving, and positioning drums compared to manual methods. For example, drum lifters and clamps enable a single operator to manage drums that would typically require multiple workers, reducing labor needs and freeing up personnel for other tasks. Mobile drum handlers enhance workflow by quickly transporting drums across different areas of a facility, cutting down on waiting times and keeping production lines running without delays. The precision these tools offer also lowers the risk of errors and rework caused by improper placement, which helps maintain smooth operations. Additionally, equipment designed for quick attachment and release saves valuable time during drum changes. By minimizing downtime from injuries or drum damage, this streamlined approach boosts overall throughput and productivity in warehouses and plants.
- Specialized equipment speeds up drum lifting, moving, and positioning compared to manual methods.
- Drum lifters and clamps allow one operator to handle drums that would otherwise need multiple workers.
- Faster drum handling lowers process bottlenecks and keeps production lines running smoothly.
- Precision in placing drums reduces errors and rework caused by improper handling.
- Mobile drum handlers improve workflow by moving drums quickly across facility areas.
- Streamlined drum movement reduces waiting times and increases throughput in warehouses and plants.
- Equipment designed for easy attachment and release saves time during drum changes.
- Using the proper tools reduces downtime caused by workplace injuries or drum damage.
- Operators can focus on other tasks as drum handling becomes less physically demanding and more reliable.
- Efficiency gains contribute to improved overall productivity in industrial and storage environments.
3. Improved Ergonomics and Reduced Physical Strain
Ergonomic drum handling equipment plays a key role in reducing the physical strain workers experience during drum tasks. By limiting the need to bend, twist, or adopt awkward postures, this equipment helps protect the back, shoulders, and arms from excessive stress. Features like adjustable height settings allow the equipment to be tailored to each worker’s comfort, which reduces fatigue and supports better posture throughout the shift. Tilt and rotation functions make pouring or mixing easier without manual effort, cutting down on repetitive lifting motions that can lead to cumulative trauma disorders. Using ergonomic drum handlers also means workers take fewer recovery breaks, stay more focused, and are less prone to fatigue-related mistakes or accidents. Over time, these benefits contribute to a healthier workforce with fewer chronic pains and longer career longevity.
4. Space Optimization for Better Drum Storage
Drum handling equipment plays a key role in making the most of available storage space. These tools allow for precise placement of drums, even in tight spots, narrow aisles, or high shelves that would be challenging to reach manually. Hydraulic and mechanical handlers support safe stacking, which helps maximize floor space without risking drum instability or damage. Organized and compact storage reduces clutter, making it easier to locate and retrieve specific drums quickly. For example, drum rackers enable fast access without disturbing other stored drums, improving workflow efficiency. By optimizing storage layouts, warehouses and plants can increase their inventory capacity without the need to expand their physical footprint, ultimately saving on facility costs. Additionally, well-planned storage setups supported by proper equipment reduce the chance of drum damage caused by overcrowding or improper stacking, contributing to safer and more efficient operations overall.
5. Long-Term Cost Savings from Using Drum Equipment
Investing in drum handling equipment helps reduce long-term costs by lowering injury-related medical and compensation expenses. When workers handle drums safely with proper tools, injury rates drop, which also decreases insurance premiums and related administrative work. The equipment itself is designed for durability, minimizing the need for frequent repairs or replacements, which saves money over time. Efficient drum movement speeds up operations and cuts down on downtime caused by bottlenecks, helping companies avoid costly delays. Better organization and space management with drum handlers can prevent the need for facility expansions, reducing overhead costs. Additionally, minimizing drum damage lowers expenses tied to product loss, cleanup, and replacing damaged drums. Standardized equipment simplifies training, saving on related costs, and improved workflow efficiency means labor resources are used more effectively, reducing overtime pay. Altogether, these factors contribute to a solid return on investment through safer, smoother, and more cost-effective drum handling processes.
6. Protection of Product Quality During Handling
Using secure drum handling equipment greatly lowers the chances of accidental drops or impacts that can damage drums. When drums remain intact, the risk of leaks, contamination, or exposure to the environment is minimized, helping to keep the product inside pure and safe. Features like smooth tilting and rotation allow for controlled pouring, preventing spills and waste. By avoiding drum deformation, seals and closures stay secure, which is crucial for maintaining product integrity. Proper equipment also helps prevent cross-contamination between different contents and external materials, especially important when handling sensitive or hazardous substances. This not only protects product quality but also supports compliance with safety and industry regulations. Additionally, reducing product loss through careful handling improves overall yield and cuts down on waste disposal costs. Consistent, careful handling ultimately helps preserve brand reputation by ensuring the product reaches customers in the best condition possible.
7. Versatile Drum Handling Tools for Various Tasks
Drum handling equipment offers a range of specialized tools designed to meet different operational needs efficiently. For example, drum rotators allow for mixing or blending contents without manual effort, which is especially useful in industries where consistent product quality matters. Drum cradles and tilters make pouring and dispensing liquids safer and more controlled, reducing spills and waste. Transporting drums is easier with mobile drum handlers and dollies, which help move heavy containers smoothly across work areas. Forklift attachments add another layer of flexibility, letting companies use their existing forklifts to lift and move drums without extra machinery. Specialized clamps can securely grip drums of varying diameters and materials, whether steel, plastic, or fiber, adapting to the specific drum type in use. Many of these tools have adjustable features, allowing workers to customize their setup depending on the task, from lifting and storage to dispensing. Combining multiple pieces of equipment enhances the workflow, making handling safer and more efficient. This versatility ensures that businesses can adapt quickly to changing demands while maintaining smooth and safe operations throughout different drum handling stages.